Organizational Communication | Implementing Change in a Reengineering Project
- Charlotte Tenebrini Steckart
- Feb 5, 2024
- 21 min read
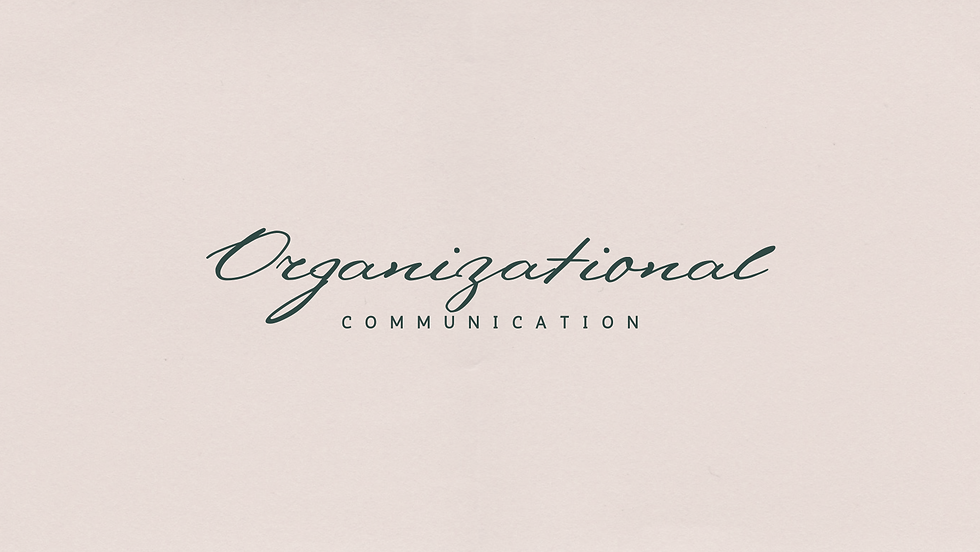
University of Wisconsin- Green Bay
Caitlyn B, Kirstynne Hock, Kallie Snowtala, Charlotte Tenebrini Steckart
Executive Summary
The purpose of this paper is to delve into the communication plan we have created for a reengineering project. In this paper we explain our communication plan that we created by analyzing the case through a KISS Chart focused on the employees and who they are, a SWOT analysis of the change, and an audience analysis. The paper also focuses on how the business goals coincide with what our communication plan looks like. Finally, this paper will walk you through our step by step plan on implementing the new changes for the paper mill.
Case Analysis
The purpose of this case is to design a communication strategy that fosters a smooth transitioning for a reengineering project. Firstly, there are 1,000 employees who work at the power plant all of which together work on 20 different machines. The people working here consist of the plant manager, the engineers, crewmembers, Dr/ mechanics and other employees. In this paper when we write team members, we are referring to everyone as a collective. They have only reengineered one machine so far. Because of this two positions will be eliminated, but affected people will just move to different positions in the plant. The whole revision will take 3 weeks to take action. When production employees are confronted with quality problems, they often blame others further up the production line. The plant manager supports this change, but is letting the production engineer and department head to plan the entire change. The company in the past has been very successful financially and continues to grow.
Kiss Chart
When going over this case the KISS chart it was helpful to understand the team members better. First is the crew members that will be directly affected with this change that is going to happen. What we know about the crew members is There is going to be fewer employees because they will be switching roles due to the fact that this position is getting laid off. What we can infer about them is that the crew members will learn a new position because their role in the company will be changing. Due to this change they will be getting more tasks because they will be learning different roles to work with. What the company can do for them is to help them better understand their new role. What not to do is just putting these crew members in the new position without any idea on what to do.
Next will be the engineers who will be the main designers of the Machinery that will be put on the field when the change happens. What is known about the engineers is that they have a large workload with not only having the pressure to fix all the machinery but also because this is their project that will be out on the field in the company in three weeks. What we can infer about the engineers is that they are the ones who will fix any of the problems the machines will have during the change and even after the change. What we can do to help out when need be. This can be when a machine needs fixing an employee might be able to step up and help out by helping fix the machine or going to another position and work on that while the machine is being fixed. When you share the knowledge on how a machine works with other employees it can help the engineers out when their work load is full and they need help. What not to do is expect the engineers can do it all. This can lead to a burn out of the employee or a slow in production.
Employees which are the front office, marketing etc.. are next in line and what is known about them is that they can have more paperwork with the change coming and going all the crew members in their new positions. This can lead to more responsibilities with helping make sure everything runs smoothly up front and helping out on the field when need be. What is inferred about the employees is that they will have more roles throughout the company and have to learn them. So what is that they will have more responsibilities in the company when the change happens. What not to do for the employees is to demand that problems and change be fixed fast. When you demand results right away they will not always workout. It’s not good for the team members to expect the employees to know their new roles right away because it will take some time and it will need some patience and team work to understand the new roles.
After the employees comes the Dr./Mechanics. The DR./Mechanics are the ones who will be fixing the machinery when there is a problem. What is known about the Dr is that they have a pressure to have the machines be fixed at a timely manner. This leads to what is inferred, which is that they fix the machines. What can be done to help the Dr is to help them out and understand their new role. Employees can be up on to the Dr and might need help learning their new role. What not to do when it comes to the DR. is to demand that the machine be fixed right away.
Last in the company is the plant managers of the company. What we know about the plant manager is that they are the ones that are in charge of the change that is happening. They are also the ones that run the paper mill. What is inferred with the plant manager is that they are in charge of all the change and how they will go about the new change. What to do to help out the plant manager is having them help to understand all the other team members' new roles. If any of the team members have any questions they can help them solve the questions or problems. What not to do with the plant managers is having them not help the employees understand their new roles and just assume they know anything about their new role.
SWOT of Change
In the SWOT of the change it was determined that their strengths were more efficient work with having the employees learn new roles and understanding different roles to help others out when needed can lead to overall benefits for the company. This can be if an employee is busy or has too much others can help out because they will understand the different roles and can in turn have more paper be made. This can help benefit the company by making more profits. It can also help to create more collaborative relationships within the company. If the employees know more of the new roles then this can help the employees collaborate in their roles to produce more paper and get more profit and to work to induce the workload on one person. When learning the new roles it can have paper be junked because there will be trial and error with learning a new position can be a weakness for the company. It might take awhile for the employees to learn and adapt to the new change. Having the plant manager be a go with the flow can create untrust with the company. If there is not a lot of help in the change and just having it be we will see what happens and go from there can be a big weakness for the company. With strengths and weaknesses there are going to be opportunities for change. This can be more efficient in the new roles. This can increase the revenue of the paper that is made. This change allows opportunities for the employees to grow in their new positions. With all of the strengths, weaknesses and opportunities there are going to be threats in the new change. The team members' roles can be on the line with losing a position and getting a new one in the company. This can also cause a push back of the employees not wanting to change positions and learning new roles. Employees might think this change is wrong and want to push back because the unknown of change can also lead the employees from freaking out when hearing about being moved to different roles in the company.
Audience Analysis
When going over the audience analysis of the company Engineers who design the machinery will be affected because of the large workload they are going to have with designing the machinery. They will also have pressure on the success of new machines when the change comes. It can be a success or it can fail and have the pressure to make sure it is successful. The lions in the group to the engineers is the machine company because they have to have all the parts, and make the machine. When it comes to channels preferred for communication its going to be face to face and email. With email it can send out an agenda of when the machine is coming and if there is any confusion face to face it is good to answer the confusions and have the engineers better understand. What the engineers know is working out all the details. Which can learn to concerns they might have which will change work out. Having the communication objectives by making sure that the communication line is open and functioning so engineers feel comfortable bringing up any future problems.
Then the crew members who are Directly affected Working on the machines. This can affect them by having them learn a new role. With the position being affected can lead to less employees in that role and making them have a higher workload or more responsibility. The lions to this group would be time. The best channel for the crew members to communicate is face to face and email. With the change being new a lot of information is going to be thrown out so an email to let them know about the change is good but there is going to be confusion and misunderstanding. This leads to having a face to face meeting to communicate the confusion and misunderstanding by answering any questions that the employees have. They know the machines the best and how to fix them. With the crew members being affected they will be afraid of the security of the new position they will be in. It can also have fear of the new crew members coming to run the machines and not knowing the role which can lead to refusal of a new role. The best way to communicate with them is to emphasize their new role and their responsibilities and make sure they are comfortable in their new position.
After the crew members there is the Dr./Mechanic who fixes the machine. Dc. will be affected by the change because they have Pressure to fix machines in a timely manner. The lions to the Drs. could be an employee not agreeing on the way they fix things or the timely manner. The best channel for the Drs. to communicate is face to face and email. With the change being new a lot of information is going to be thrown out so an email to let them know about the change is good but there is going to be confusion and misunderstanding. This leads to having a face to face meeting to communicate the confusion and misunderstanding by answering any questions that the employees have. The Doctors are known for the machines and how to fix them. They even know about the change and what is happening. Just like the other groups the DR will have concerns for the change. Their concerns might be that they can't fix the machines in a timely manner and make sure their position is secure in the company. Their way to communicate their objective to the doctors is To make sure that they are able to focus on their new jobs with the new changes implemented.
After the Dr. comes the Employees that are the front office, marketing etc.. The employees will be affected by the change because they will have more paperwork due to the change happening and will lead to having more responsibility with the change. The lion in the employee group is tina. The best channel for the employees to communicate is face to face and email. With the change being new a lot of information is going to be thrown out so an email to let them know about the change is good but there is going to be confusion and misunderstanding. This leads to having a face to face meeting to communicate the confusion and misunderstanding by answering any questions that the employees have. What the employees know is that they Assume a change is happening. With knowing a change could happen there is going to be concerns for them. The concern for the employees is that things will be communicated to them. The way to communicate to the employees for their objective on the change is to To keep things functioning as normal.
Lastly the plant managers will be affected by the change because they have pressure to run a successful plant. The plant managers also have Pressure to make sure change is happening. The lions to the plant managers are the Engineers because they are the ones who design the machines for the change. The best channel for the plant managers to communicate is face to face and email. With the change being new a lot of information is going to be thrown out so an email to let them know about the change is good but there is going to be confusion and misunderstanding. This leads to having a face to face meeting to communicate the confusion and misunderstanding by answering any questions that the employees have. Plant managers know about the change and what is going on. They also know about what employees will change roles and who will stay in the same positions. Plant managers are in charge of the change and making it happen can lead to them having concerns of the change. Which can be How their staff will react to the change. Even having blame for changing the employees' roles. The plant managers way of communication objectives to the other employees are To be able to have a plan in place so that it is an easy transition for the entire team
So What?
Helping to understand each role for the team members in the company. It helps to better understand how the roles fight into the communication plan. It has a better understanding of each team member and what their roles are. Helping to understand what roles in the new change that will be happening fast. Lastly it a better Understand to what group will be affected the most and how to translate information appropriately for each group
Business Goals
For this case, we chose three business goals that will help make the transition of the company with the change nice and, hopefully easy, for the team members. The first goal is to have an overall smooth transition to maintain a quality work environment for all. The second is to have efficiency, quality, and economic stability. The last goal is to combine the two and to create a quality work environment to maintain efficiency, quality, and economic stability. By combining these together, this will create a sense of harmony along with the change and ease the team members' minds as they go through this time.
Communication Goals
The communication goals for the company during this change are split up into four parts. First, we want there to be effective communication between upper management, the plant manager, and subordinates. This will help everyone understand what is happening. This leads into the next goal– have a mutual understanding of why the company needs this change. We understand that there will be some team members that disagree with the change, but we want to make sure that everyone knows that this change will happen, regardless of if they approve or not. This is what is best for the business at the time, so this is what will be happening. Which segways into the third goal of having a mutual understanding of the business and what it is. Lastly, we want to have a smooth transition between past and future communication styles once the change comes into play, in three weeks.
Communication Plan
The communication plan that we developed for the reengineering project is to set up face to face meetings with each group, when the launch of the reengineering is three weeks out. We want to acknowledge that this is a time sensitive situation. First we will send emails to each group to inform them of a meeting they need to attend. We will then meet with each group individually starting with the doctors and mechanics then the crew members, employees and engineers. Meeting with each group individually helps to acknowledge that each group is in a different stage and you can change how you deliver the message. We would like to meet with the groups in this order because it goes from least affected to most affected. We hope that this will help elevate some confusion and some rumors that may spread among the company. Once all initial meetings are wrapped up we would like to hold another meeting with all of our team members to address further concerns and questions.
First, it is important to identify what stage each of these groups of people will be in. This will help us understand the individuals and how they are feeling. Also, give us more insight on how to deliver the message to them. We believe that the Plant Manager will be in the acceptance stage because he has been behind the reengineering project and supporting it from start to finish. The next group is the engineers, they are also in the acceptance stage. The engineers have been the ones that are doing the reengineering. They have been doing alot of the work and are ready for the machines to hit the floor for more efficiency. Now, the crew members feel they are in the denial stage. They will most likely be in the denial stage because they are going through the change and can’t believe that they will be changing roles. The next group we have is the DR/ mechanics. This is the group that is being affected the most, their role is being eliminated but they are not losing their position in the company. We feel that they will be in the anger and bargaining stage. We feel this because they will want to try and keep their current position and be upset about the change that is happening in the company. The last group is the employees, they will be in the denial stage. This group is the least and indirectly affected due to the change. The employees will be in denial of what changes are coming and the way they will have to change as well.
Strategies and Tactics
Deciding what stage each group was in helped us develop our strategies and tactics. For many our strategies and tactics are very similar. For each group or strategy is to email each group to inform them of what time they are meeting starting with the Dr/ mechanics. This meeting like said earlier is being held three weeks prior to the launch of the reengineering project. Where things differ for each group is the tactics.
The tactics for the Dr/mechanics is to meet with this group first face to face. Explaining to them the reengineering project and that they still have a role in the company but that the role is changing. The reengineering project is going to help make the company more efficient and profitable. It is important that we approach this group with care because they are going to have a hard time with this transition. We would also like to open it up to any questions, comments or concerns this group may have. These questions, comments or concerns will be written down for them to be addressed in a later meeting. We want to make sure that they know they are being heard and their concerns are important to us. At the conclusion of the meeting we will send a recap email to go over everything that has been discussed in the meeting and a date for the second meeting.
Next, the tactics for the crew members are in the denial stage.We need to approach them and understand that there may be some confusion with this group of people. We will send out an email with a meeting time for this group of people three weeks prior to reengineering launch. There will be a face to face meeting held to discuss details of the reengineering project and discuss that some roles may be changed within the company. Once everything is explained we will write down any questions, comments and/or concerns the group has to be addressed later. A follow up email will be sent to this group to recap the meeting and a date with a full team member meeting.
The next group that we will talk to is the employees, this is all of our front end people. This group is more indirectly affected but we feel they are in the denial stage. An email will be sent to the employees for a meeting time. In their face to face meeting it can be more relaxed discussing the reengineering that is happening because they aren't affected directly. After everything is explained there will still be time for this group to express concerns and questions and they will be written down. We will send a follow up email to this group to recap the meeting and to send a date to them for a full team meeting.
The last group we will meet with is the engineers. They are in the acceptance stage. The engineers will receive an email with a meeting time for their face to face meeting. In the meeting with the engineers we will inform them that everyone has been made aware of the reengineering that is taking place. They will be asked for their help in this transition but their concerns and questions are still important as well. They will be sent an email to recap everything and a date for the full team member meeting.
The last thing that we would like to do is hold another meeting with all team members. This meeting will take place one week prior to reengineering launch. In the meeting we will again recap the reengineering project and the benefits along with reassurance that no one is losing their position in the company. In this meeting we will also be addressing the questions, comments and concerns we took down in the initial meeting to help address things people still have questions about. This is to help make the transition as smooth as possible and alleviate any further concerns.
SWOT of Communication Plan
After putting our communication plan together, we wanted to find out what strengths, weaknesses, opportunities, and threats would come out of it. We compiled a SWOT analysis of the plan and this is what we found. A couple strengths of the plan is that there is a separate strategy and tactic in place for each team member to best suit them. This will help the company communicate the change most efficiently to the team member based off of the stage of grief they may possibly be in, as we stated previously. With strengths, come weaknesses. We found that backlash will happen, no matter what. It is inevitable that backlash and pushback from all the team members is possible. We think this will be due to the fact of us choosing to talk with the Doctors first and that the change is happening regardless of what anyone says. Team members may think that the company is favoring the Doctors since they were spoken to first. Some opportunities within this communication plan is that each email that goes out to the team members is specific to that group. This will help prevent backlash and pushback as much as possible. Also, with the way the plan is set up, we have given time and resources to ask questions and help get answers regarding the change. Lastly, the threats that are posed with this communication plan are the resistance and adversity that will be faced from the team members. This goes back to the backlash and pushback that will possibly happen during the change. And as with any change, there are always unknowns as to what will happen in some areas, so not knowing everything that will happen or potentially happen, will be a threat to the company and to the communication plan as a whole.
Rejected Solutions
Three potential solutions that we talked about during our process that were rejected in the end were; spray and pray, tell and sell, and feedback loop. Starting off with a feedback loop, it is not what one might think. When we were discussing our solutions we wanted to hear feedback, but we did not want the whole communication plan to be based around the idea of feedback. Yes, we still have an opportunity for feedback in our plan, as most plans should. But, this change is going to happen regardless of any feedback a team member may give. This is why we rejected the solution of having one big feedback loop altogether. It would not have done much if all we were getting was feedback, since that is not what the goal of the communication plan was. Spray and Pray was another suggested solution that we talked about as a group. We decided against this because the team members did not need to know all of the information about the change. They only needed certain information that pertained to them. Which leads me into the last rejected solution, Tell and Sell. This seemed like the perfect solution at first, but as we continued we realized that this option did not allow for any feedback. This solution is focused on giving out limited information and ‘selling’ the team members on the change, which is basically what we are trying to do. But we want the option of feedback. Like we stated, this solution did not offer much, if any, feedback, which is why we decided against it.
Lessons Learned
Our three lessons learned during this case study was that the business and communication goals helped assist us in developing our communication plan. Once we understood what the goals were, we were able to make a plan based on what the company wanted and also what the company needed. Throughout this process, we understood how to communicate effectively and change our communication skills based on the stage of grief an individual or group may be in. This will be really important in the real world, because not everyone reacts the same to one communication style. There will be times when it needs to be changed up a little bit in order to transmit a message. Lastly, this change was happening in three weeks, so there was no cutting corners. It was very time sensitive and everything had to be done quickly and efficiently to make sure everyone was on the same page and knew what was going on in the company.
Appendix
The first paper mill north of the Alps was established in Nuremberg by Ulman Stromer in 1390;
Pepper mills, sometimes referred to as pepper grinders, are a common kitchen accessory designed to grind peppercorns into a fine powder used to season foods.
Paper mills are factories dedicated only for the production of paper and paper-related products.
They inherited their name from the wood mills, who were in early 19th century slowly transformed into manufacturing facilities for processing wood into form that is suitable for the production of wood pulp.
England began making large supplies of paper in the late 15th century and supplied the colonies with paper for many years.
Finally, in 1690, the first U.S. paper mill was built in Pennsylvania. At first American paper mills used the Chinese method of shredding old rags and clothes into individual fibers to make paper.
Paper mill runs all 24 hours in a day. The workers work in three shifts of eight hours each.
Typically high pressure steam is run through a turbine to generate electricity, then the lower-pressure steam that results is used for the paper-making process
Recycling has always been a part of papermaking.
By the early 20th century, paper mills sprang up around New England and the rest of the world, due to the high demand for paper
At this time, there were many world leaders of the production of paper; one such was the Brown Company in Berlin, New Hampshire run by William Wentworth Brown.
At this time, there were many world leaders of the production of paper; one such was the Brown Company in Berlin, New Hampshire run by William Wentworth Brown.
Paper mills can be fully integrated mills or nonintegrated mills.
The modern paper mill uses large amounts of energy, water, and wood pulp in an efficient and complex series of processes, and control technology to produce a sheet of paper that can be used in diverse ways.
Modern paper machines can be 500 feet (150 m) in length, produce a sheet 400 inches (10 m) wide, and operate at speeds of more than 60 miles per hour (97 km/h).
The two main suppliers of paper machines are Metso and Voith.
First paper mills equipped with the Fourdrinier machines were established in Frogmore,
According to Timothy Hugh Barrett, paper played a pivotal role in early Chinese written culture, and a "strong reading culture seems to have developed quickly after its introduction, despite political fragmentation.
Indeed, the introduction of paper had immense consequences for the book world. It meant books would no longer have to be circulated in small sections or bundles, but in their entirety.
Frogmore Paper Mill is a working paper mill situated in Apsley, Hertfordshire, near Hemel Hempstead.
The mill is on an island in the River Gade, which forms part of the Grand Union Canal.
The mill is on an island in the River Gade, which forms part of the Grand Union Canal.
The mill is run by The Apsley Paper Trail, a charitable organization, and operated as a visitor, education and community use centre.
Eleven full-time staff are employed at the mill.
For most of the 19th century, the mill was owned by the Grand Junction Canal predecessor of the Grand Union Canal
Engineer facts
Engineers are responsible for all upkeep of the machinery involved in paper making process
Developing maintenance schedules
Analysis of equipment and reasons for issues
Responsible for chemical tanks
Corrosion management
Operating tasks for the engineers goal is to create as much as possible as cheaply as possible and as safely as possible
“An engineer could be tasked with making the papermaking process more efficient by increasing production or eliminating wastage.”
“Chemical management is often dealt with by the engineers in the pulp and paper industry”
An engineer might also be responsible for the design of control systems. These systems are used, for example, to shut down the papermaking process if it goes outside safe operating parameters. These control systems are used to safeguard people and equipment.
Chemical engineers are needed
Industrial engineers are needed
Electrical engineers
Process engineers
“As of May 2019, there were 3,700 engineers employed in the pulp and paper industry in the United States. Although there are always engineers retiring, 3,700 jobs to compete for in a country of 330 million is not a lot.”
“Pulp and Paper Technician / Engineer training is a valuable first step on a career path. A high school diploma or GED Equivalent Certificate is required for all participating students.”
The program teaches them to understand how paper is made
They will also be able to teach other people
“The Process Engineer's primary responsibilities are to support problem solving efforts mill-wide through planning and conducting trials directed toward, productivity improvement, product development, quality improvements and cost reduction for paper manufacturing.”
Plant manager
Need to have a bachelor's degree in engineering– paper science or related field
“Drive continuous improvement and operational excellence”
Plan, organize, direct, and run optimum day to day operations to exceed customer expectations
Increase production, assets capacity, and flexibility while minimizing unnecessary costs and maintaining current quality standard
Be responsible for production output, product quality and on-time shipping
Allocate resources effectively and fully utilize assets to produce optimal results
Implement strategies in alignment with strategic initiatives and provide a clear sense of direction and focus
Monitor operations and trigger corrective actions
Share a trusting relationship with the workgroup and recruit, manage, and develop plant staff.
Collect and analyze data to find places of waste or overtime
Commit to plant safety procedures
Develop systems and processes that track and optimize productivity and standards, metrics, and performance targets to ensure effective return on assets
Address employees’ issues or grievances and administer collective bargaining agreements
Influence and learn from below
Stay up to date with latest production management best practices and concepts
Proven managerial experience
Adequate knowledge of business and management principles
Familiarity with industry standard equipment and technical expertise
Be knowledgeable of safety, quality, productivity, demand creation, inventory, and stewardship process
Computer literacy
Ability to create accountability and to lead by example
Proven managerial experience
Optimize paper machine schedules to maximize the mill’s production while continually increasing paper machine uptime % and productivity while reducing off quality
Receive many bonuses and benefits
Overlook the whole staff
Operating machinery
Cylinder machines are used to make paper
Fourdrinier machines are used to make paper
Change is scheduled to take place in 3 weeks
There are 1,000 employees assigned to 20 machines
Two jobs will be eliminated
Comments